05/01/2023
Energy Efficiency for Sustainable Aerospace Manufacturing
As the demand for air travel continues to soar, the aerospace industry faces a critical challenge: How to meet this demand while minimizing its costs and environmental impact.
One key solution is to improve energy efficiency in the manufacturing of aircraft and aerospace components. By reducing energy use and related emissions, we can not only protect the planet, but also save money and improve the bottom line for aerospace manufacturers.
In this blog post, we will delve into the current state of energy use in the aerospace industry. We will explore the opportunities for improvement, the challenges and solutions for improving energy efficiency in this energy-intensive sector.
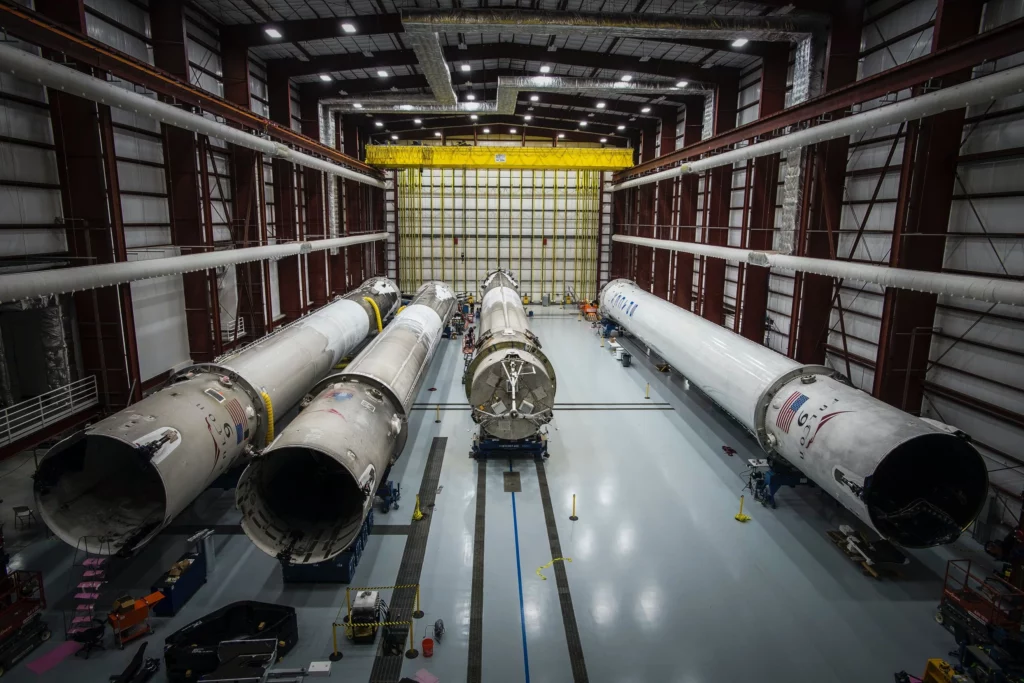
Most popular
Energy is an important resource for aerospace manufacturers; it is the means by which raw materials are transformed into useful products.
The aerospace industry uses large amounts of energy. Actually, energy use occurs at every stage of the manufacturing process. From the initial design and engineering of aircraft to the production of components and assembly of the final product, energy is required at every step. The transportation of passengers and cargo also consumes significant amounts of energy, particularly in the form of jet fuel.
The Environmental Impact
The environmental impacts of this high energy use are quite significant. Carbon emissions from the use of fossil fuels in the aerospace and aviation industry contribute to climate change and have far-reaching effects on the planet.
Global aviation accounts for:
- 1.9% of greenhouse gas emissions
- 2.5% of CO2 emissions
- 3.5% of effective radiative forcing* – a closer measure of its impact on global warming.
* Radiative forcing measures the gap between incoming energy and the energy radiated back to space.
The first stat refers to 2016, and the latter two refer to 2018, the latest years for which such data are available (According to Our World In Data).
Here’s a fact: Air travel is hard to decarbonize.
There are some design concepts developing, such as Airbus’ plans to have the first zero-emission aircraft by 2035, using hydrogen fuel cells. Electric planes may also be a viable concept.
But we don’t have a proven solution to tackle aviation yet.
However, what we can act on and decarbonize now, is the aerospace manufacturing field.
The production of aircraft and aerospace components generates hazardous waste and emissions that harm local air and water quality. These impacts have serious consequences for both the natural environment and human health.
The Financial Impact
The financial impacts of high energy use in the aerospace industry are also significant. Energy costs are a major expense for aerospace manufacturers, and reducing energy use will lead to important cost savings.
In addition, improving energy efficiency can improve the financial performance of aerospace manufacturers by increasing profitability and competitiveness.
In today’s global market, companies must be efficient in order to stay competitive.
By demonstrating a commitment to sustainability and energy efficiency, aerospace manufacturers can differentiate themselves and appeal to environmentally-conscious consumers.
Challenges to improving energy efficiency in Aerospace Manufacturing
Here are a few common challenges that aerospace manufacturers face when trying to improve their energy efficiency:
- High upfront costs: Implementing energy-efficient practices often requires a significant investment in new equipment or technologies. This can be a challenge for aerospace manufacturers, especially for smaller companies with limited financial resources.
- Employee training and buy-in: It is important for employees to be trained on new equipment or processes and to understand the importance of energy efficiency. This can be a challenge, particularly if employees are resistant to change or are not fully on board with the energy-efficient initiatives.
- Complex supply chain: Aerospace manufacturing often involves a complex supply chain with multiple suppliers and subcontractors. Coordinating energy-efficient practices across this supply chain requires strong communication and collaboration.
- Regulatory barriers: There may be regulatory barriers or challenges to implementing energy-efficient practices in the aerospace industry. For example, there may be safety or environmental regulations that must be followed, which can add complexity to the process.
By overcoming these challenges, aerospace manufacturers can successfully implement energy-efficient practices and improve their energy efficiency. But how can they do it?
Improving Energy Efficiency in Aerospace Manufacturing
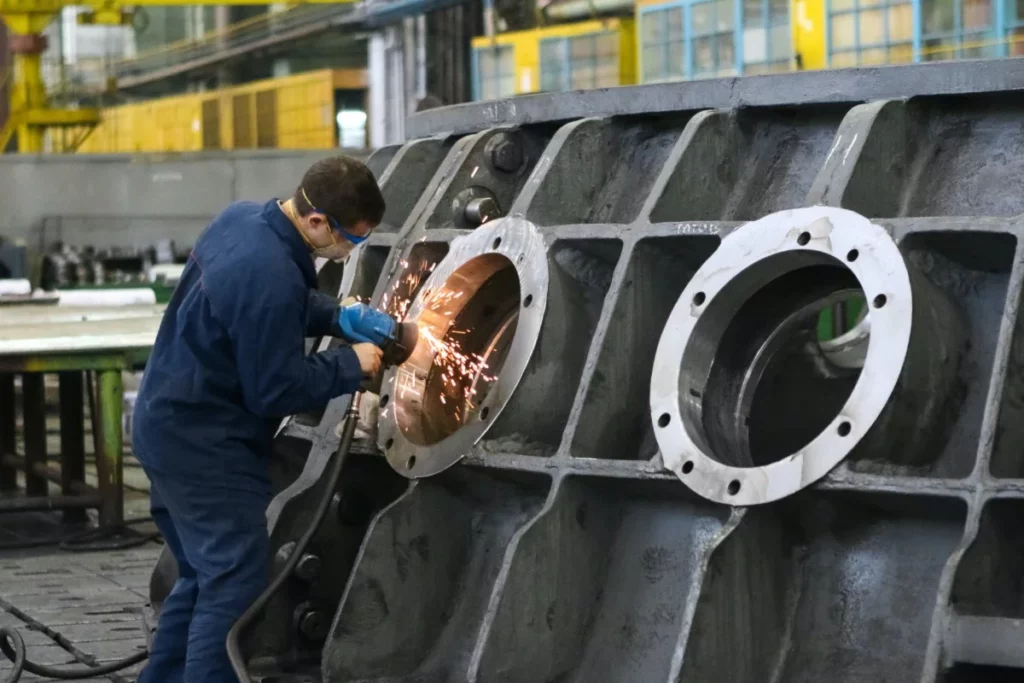
Here are some best practices for improving energy efficiency in aerospace manufacturing:
- Design for energy efficiency: One key way to improve energy efficiency in aerospace manufacturing is to design aircraft and components with energy efficiency in mind. This can involve factors such as aerodynamics, weight, and engine efficiency, which can all impact fuel consumption and emissions.
- Adopt lean manufacturing principles: Lean manufacturing is a set of principles that focus on reducing waste and improving efficiency in the production process. This can involve eliminating unnecessary steps, streamlining processes, and using more efficient equipment and techniques.
- Invest in energy-efficient equipment: Upgrading to energy-efficient equipment can help reduce energy use in the manufacturing process. This can include everything from energy-efficient lighting to more efficient production machinery.
- Implement energy management systems (EnMS): Energy management systems can help companies track and monitor their energy use, identify areas for improvement, and set and track energy-saving goals.
- Utilize renewable energy sources: Another way to reduce energy use and emissions in aerospace manufacturing is to switch to renewable energy sources, such as wind or solar power. This can help reduce a company’s reliance on fossil fuels and reduce its environmental impact.
- Promote employee engagement: Encouraging employee engagement and buy-in is important for the success of any energy-efficient initiatives. This can involve training employees on the importance of energy efficiency and involving them in decision-making processes related to energy-saving measures.
By adopting these best practices, aerospace manufacturers can significantly improve their energy efficiency and reduce their environmental impact. It is important for companies to carefully consider their specific needs and goals when implementing energy-efficient practices and to develop a plan that works for them.